Table of Content
How to Solve Last-Mile Delivery Challenges in 2025?
Table of Content
Online shopping has thoroughly displaced in-person shopping. In fact, more than 80% of consumers in the US are shopping online!
With a huge chunk of customers preferring the online experience, last-mile deliveries powered by cutting-edge fleet management technologies have become indispensable to businesses.
One report projected that the global autonomous last-mile delivery market would reach $84.72 billion by the end of 2030.
In fact, before you read this sentence, Amazon would have already shipped some 100 parcels nationwide!
However, while last-mile deliveries are on the rise, so are the challenges associated with them. For instance, did you know that last-mile deliveries account for more than 50% of all shipping expenses?
In our experience, there are several reasons for this:
Rising costs of delivery
Delays in delivery
Inefficient routing and lack of route optimization
Lack of transparency
Outdated delivery tools and technologies
So, how can we overcome last-mile delivery challenges in 2025?
In this blog, that’s exactly what we’ll talk about. We’ll discuss the top challenges to last-mile delivery and how we can solve them.
What is the Last Mile Problem?
The last-mile challenge exists due to a simple contradiction of online shopping: while customers want fast and convenient doorstep delivery, businesses want to minimize the cost of last-mile delivery.
The last-mile delivery challenge is further compounded by several factors:
High-cost deliveries in low-demand locations
Logistical issues such as the unavailability of vehicles
Inefficient route optimization
Poor collaboration with local delivery partners
So, what are the most critical challenges to last-mile deliveries? Let’s find out…
What are the Top Challenges to Last-Mile Delivery in 2025?
Over and above the cost of doing business, we face six critical problems with respect to last-mile deliveries:
1. Inefficient Delivery Routes
Say you have 5 deliveries to make in a city, all in different areas. Now, the most efficient way to complete all deliveries would be to create an optimal route:
Starting with the farthest delivery
Working back to the delivery point closest to your warehouse.
But here’s the issue: the customer who lives the farthest from your warehouse might only be available to accept the delivery at a specific time. This can be a major problem if you need the recipient to be present at the time of delivery.
Our problem becomes even more complicated for B2B deliveries or when we deliver high-value products such as pharmaceuticals, hazardous materials or expensive items.
2. Missed Deliveries
We all know that a missed delivery = a dissatisfied customer.
One reason businesses miss deliveries at the last-mile stage is that the customer is unavailable during the delivery. Other reasons include fleet breakdowns, driver unavailability, or logistical bottlenecks that lead to delays.
If you’re operating a retail or a B2B enterprise that relies on remote purchases, you know how critical missed deliveries are to business success. They affect operational efficiency as much as customer satisfaction.
3. Driver and Asset Management
Drivers and assets represent two of the most important resources to businesses. The first is human capital; the second is long-term capital investment.
Managing both efficiently is key to operational success and long-term business sustainability.
In our experience, they’re also the hardest to manage. For instance, drivers might require:
Route change instructions
Vehicle breakdown assistance
Technical training for technology integration
Similarly, delivery fleets also require a lot of attention:
Periodic maintenance
Technological upgrades
Replacement with next-generation vehicles
In short, ensuring driver and asset health are structural problems we must solve in order to prevent other problems from arising!
Looking to streamline fleet management and enhance driver coordination?
Optimize operations with seamless fleet management through our custom web & app solutions.
Get Started Today!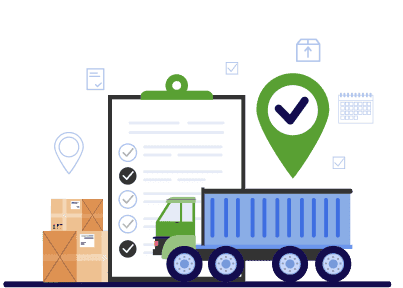
4. Warehouse-to-Customer Proximity
Did you know that Amazon has more than 100 fulfillment centers across the United States? These fulfillment centers manage more than 1.5 million deliveries every day!
Now, it’s one thing to sell your products on Amazon: they’ll eat up a part of your revenue in return for their logistics services.
We recommend using supply chain managed services; at Green Apex, we can help you minimize delivery costs and maximize profits through these dedicated services.
But does that mean you’ll also have to set up giant warehouses throughout the country? In our experience, if you need to ship products regularly or are operating a logistics business, you might want to look into vertically integrating warehousing solutions.
These solutions are available at different scales, so you can choose how and what you want to invest in creating your own supply chain.
However, that just leads to another problem: where should you place your warehouses? Near where the customers live? But those locations might be far away from the major delivery routes that flow through the country!
In short: we face a tough choice in deciding where to place our warehouses, near the supply chains or the customers.
5. High Cost of Last-Mile Delivery
Speaking of warehouses and customers, we started our discussion with the biggest problem associated with last-mile delivery: the high cost.
Our experience with different logistics enterprises suggests that the high cost of last-mile delivery is a combination of different problems in disguise.
That is to say, the cost of last-mile delivery arises due to missed deliveries, suboptimal routes, driver + asset management challenges, and so on!
However, from another perspective, the cost of last-mile delivery is also an inherent problem.
Think about it this way: we produce our products in a centralized hub, such as a factory, a farm, a lab, or a workshop. However, our consumers live all across the country, in different states, cities and counties.
And they place their orders at different times, depending on when their needs arise.
In our opinion, the high cost of last-mile delivery has to be dealt with through a “death by a thousand cuts” approach, optimizing micro-factors that lead to the bigger problem.
6. Sustainability
Gas-guzzling fleets may be the norm, but they’re already being replaced by more efficient and cost-effective solutions. And if we don’t transition today, we’ll be ruining our missed opportunities tomorrow.
But we often mistake sustainability for “electric vehicles.” In our opinion, sustainability is about more than just the transition to EVs.
From what we’ve seen, sustainability is also applicable to packing materials, data analytics and software management. The idea is to utilize reusable materials, more efficient analytics and easily replaceable code.
In the long run, solving the deeper-lying processes that lead to expensive last-mile deliveries will help us cut more costs than surface-level problems like the kind of delivery vehicles we use.
Here’s how we helped Yatra Freight tackle its biggest last-mile challenges and streamline logistics operations.
Discover How?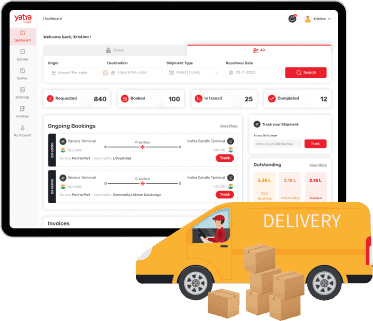
How to Solve Last-Mile Delivery Challenges?
Okay, so we’ve examined some of the most prominent challenges to the problem of last-mile delivery. What can we do to solve them? In our opinion, there are seven very good solutions we have on hand right now:
1. Route Optimization
In our experience, route optimization is the best way to solve the problem of inefficient and expensive delivery routes.
Here’s how it works: we use advanced telematics technology that combines GPS and historical data analysis to devise the most optimal delivery routes for efficient deliveries.
This helps us save time and effort, eliminate duplication, and ensure faster deliveries.
2. Autonomous Vehicles
2024 was the year AI went mainstream. In our opinion, a significant effect of AI on the logistics industry has been the rise of autonomous vehicles.
The key to autonomous vehicles is the use of Driver Assistance Systems. Advanced Driver Assistance Systems (ADAS) can help drivers with several challenges, including:
Lane assistance
Blindspot Monitoring
Forward Collision Assistance
Intelligent Speed Adaptation
Parking Sensing
Parking Assistance
The idea is to assist the driver with the most difficult and monotonous tasks to ensure driver safety and asset health.
3. Predictive Maintenance
Predictive maintenance is one of the most exciting developments in the world of fleet management. The idea is to create an algorithm that works on the basis of historical data to predict when our fleets will require routine maintenance.
The algorithm accounts for different factors, including asset age & health and route condition, to create a schedule for the maintenance of delivery vehicles.
The aim is to minimize vehicle downtime and maximize capital investment into delivery fleets.
If you’re interested in leveraging this technique, check out our insight into how predictive analytics boosts last-mile delivery.
4. Transition to EV Fleets
Electric vehicles have more than just environmental implications. In fact, they’re very good for business!
Why?
Because electric vehicles have fewer moving parts compared to conventional combustion engines, as a result, they undergo less wear and tear and, therefore, depreciation in financial value.
On the accounting side, we can also increase the amortization rate, thereby decreasing capital investment in the long run!
Going green is a win-win!
5. Real-time Communication with Customers
One of the major points of our discussion on last-mile delivery challenges was missed deliveries. It increases the logistics cost/delivery and creates unhappy customers.
The best way to solve this problem is through real-time communication with the customers!
One way to accomplish this is to mention the predicted delivery times in email updates or on the customer’s profile/dashboard. Another is to ping the customer the day before the delivery, asking for their preference for the best delivery window.
The route optimization algorithm can then take these details into account before devising the best delivery route for the next day.
6. End-to-End Logistics Management Software
Now, you must be wondering: all these solutions might be very effective. But they seem very scattered. After all, to adopt these solutions, your fleet managers need to juggle several tasks, including:
Integration of ADAS Systems
Driver management
Asset health monitoring
Real-time communication
In our opinion, the best way to integrate all these solutions in one place is to develop end-to-end fleet management software.
It will equip you with a centralized dashboard, your fleet managers with dedicated windows for different tasks, and your drivers with a real-time communication function.
Logistics Management Software: One-Stop Solution to Last-Mile Delivery Challenges
Since we’re on the subject of end-to-end logistics management software, let’s examine how it works:
1. What is an End-to-End Logistics Management Software?
A logistics management software helps you manage orders, drivers, assets and customers. It is a tailor-made solution that addresses the specific problems that you face in your logistics operations.
2. How Can a Logistics Management Software Help You?
Logistics management software can help you solve the problem of last-mile delivery challenges in the following ways:
Centralized Control Over Assets
Never lose track of your delivery assets or drivers. A logistics management software works with advanced telematics technology to help you monitor each and every driver and asset in your supply chain.
You can use this technology for re-routing, remote repairs and maintenance scheduling!
IoT Integration for Driver Assistance
Internet of Things devices are the best way to assist drivers and monitor their health on the job. Through Electronic Logging Devices, you can find out where your drivers are and in what conditions they’re operating.
To help you with compliance and driver health management, you can then design precautions like drowsiness sensors and enforced vehicle shutdowns in case of distressing situations.
Order + Inventory Tracking
Inventory is the lifeblood of a logistics business. And a logistics management system is like a blood test. It ensures that you never lose a single package ever again.
To do so, a logistics management system can leverage advanced RFID and telematics technology. So, regardless of the terrain, location and condition of your package, you’ll always know where it is. Plus, you can always share this information with your customers so they’re always in the loop…
No more unhappy customers!
Data Collection for Greater Insights
Data-driven decision-making is key to operational efficiency: logistics management software can easily integrate data collection to provide you with greater insights into your operations.
For instance, you’ll know how many extra trucks you need to have for the holiday season delivery rush. Similarly, you’ll know which assets have historically performed the best in given terrains. This can give you the opportunity to create specialized fleets for different terrains.
Data analysis through logistics management software is your key to unlocking maximum return on capital investment!
CRM Integration for Enhanced Satisfaction
If inventory is the lifeblood of your business, customer satisfaction is even more important. It’s the source of your survival, growth and long-term profitability.
Logistics software development solutions can help you integrate CRM platforms with your fleet management functions.
It functions like a clearinghouse of customer inputs and driver outputs. Remember when we spoke about real-time communication with customers? This is the secret to maintaining that communication and delivering its results to the drivers so they can ensure maximum customer satisfaction!
3. How Much Time Does it Take to Develop Logistics Management Software?
In our experience, engineering a custom logistics management software solution can take between 3-6 months. Most of the time is required for:
Data migration to the new software ecosystem
Setting up user-facing functionalities
Creating a fleet management dashboard
Training AI algorithms for route planning
The actual time will depend largely on the kind of functions you want to integrate with your logistics software.
Future-Proof Your Supply Chain With Green Apex’s Last-Mile Delivery Solutions!
Last-mile delivery problems offer a daunting challenge to the growing logistics industry.
However, technology is growing just as fast, if not faster, than the challenges we face.
At Green Apex, we work at the intersection of problems and technologies to develop ideal logistics solutions using last mile delivery analytics.
Our veteran logistics software developers have experience in working with a diverse range of tech stacks to design bespoke to your logistics needs.
So, if you, too, want to achieve maximum operational efficiency through a logistics software solution, why not connect with us for a commitment-free consultation?
We can help you develop holistic last-mile delivery platforms or engineer specific solutions to the challenges you want to overcome…
How to Solve Last-Mile Delivery Challenges: FAQs
In our experience, the biggest last-mile delivery challenges include:
1) Route optimization for efficient deliveries
2) Missed deliveries leading to increased costs
3) Driver and asset management for minimum downtime
4) Warehouse-to-customer proximity for optimal delivery routes
5) Transition to more sustainable last-mile delivery infrastructure
An end-to-end logistics management software offers us comprehensive solutions to last-mile delivery problems. Here’s how it works:
- It provides your fleet managers with a centralized control panel they can use to track drivers and inventory.
- You can use the software to analyze historical data and set up a smart maintenance schedule
- The logistics management software will help you maximize asset health and capital investment into your logistics operations
- You can also integrate route optimization and CRM solutions to your logistics software to further streamline your supply chain.
In our experience, AI is having three major effects on last-mile delivery:
- Better route planning for efficient and faster deliveries using advanced telematics
- Advanced Driver Assistance Systems for Optimal Driver Health
- Predictive analytics to ensure maximum return on capital investment in delivery fleets
Predictive analytics can help you solve last-mile delivery challenges by devising scheduled maintenance routines. Its aim is to reduce asset downtime and maximize return on capital investment by ensuring that your delivery fleet is never out of action!
Related Blogs
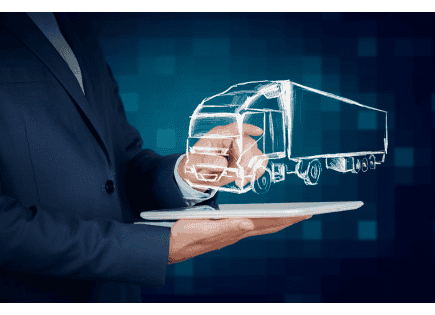
11 Cutting-Edge Fleet Management Technologies to Transform Your Logistics Business
The global logistics industry is going through an exciting, bullish period. Already worth $29 billion, it ...
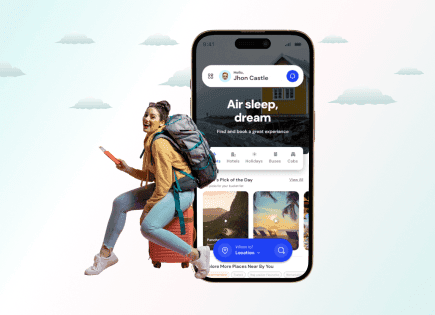
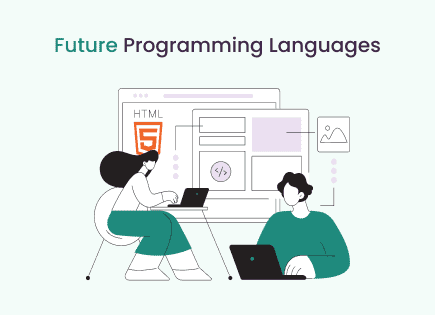
Top 17 Future Programming Languages 2025-2030
Over the past decade, our computing capabilities have improved radically and coding languages have evolved at ...